ПІРОЛІЗ МЕТАНУ ДЛЯ ОТРИМАННЯ ацетилену
Карбід кальцію отримують з оксиду кальцію і коксу в електродугових печах. Реакція сильно ендотермічна і вимагає великих витрат електроенергії, що становить суттєвий елемент в собівартості виробленого ацетилену.
Початковою сировиною для отримання ацетилену можуть служити газоподібні парафінові вуглеводні (метан, етан, пропан, бутан) і рідкі нафтові фракції, наприклад прямогонні бензини.
Вибір вуглеводневої сировини залежить від багатьох факторів, в сукупності визначають економічність процесу в цілому, від наявності ресурсів сировини, витрати енергії, виходу ацетилену і його концентрації в продуктах реакції, від кількості та вартості побічних продуктів і можливості їх рентабельного використання.
Однак промислова технологія переробки гудрону і інших нафтових залишків ще повністю не розроблена, через що цю сировину поки не використовується.
Енергетично найменш вигідною сировиною для отримання ацетилену є метан. Для його піролізу потрібно затратити більшу кількість тепла (91 ккал / моль), в той час як для піролізу етану і пропану потрібно відповідно 78 і 61,9 ккал / моль. Піроліз метану проводиться при більш високих температурах, ніж його гомологів. Однак метан використовується для отримання ацетилену на багатьох установках. Пояснюється це тим, що метан - найбільш доступний і дешевий з вуглеводнів; він є основним компонентом природного газу, і останній може застосовуватися для виробництва без поділу.
МЕТОДИ виробництві ацетиленові
Існують два методи виробництва ацетилену: старіший - з карбіду кальцію і новий з вуглеводнів.
При розкладанні утворився карбіду кальцію водою по екзотермічної реакції виходить ацетилен:
З 1 кг технічного карбіду кальцію, що містить домішки коксу, оксиду кальцію та інших речовин, виходить 230--280 л ацетилену (ця величина називається літражем карбіду). Теоретично з 1 кг чистого СаС2 має утворитися 380 л С2 Н2.
При розкладанні карбіду кальцію слід дотримуватися деяких умов для нормального протікання процесу. Реакція є гетерогенною, і її швидкість залежить від розміру шматків карбіду, особливо сильно зростаючи при використанні карбідної дрібниці і пилу. Реакційну масу необхідно перемішувати бо інакше на шматках карбіду може утворитися шар вапна, що перешкоджає повного розкладання карбіду і приводить до місцевих перегрівів. З реакційної зони потрібно постійно відводити тепло, щоб оберегти ацетилен від можливої полімеризації і розкладання.
За способом підведення тепла для проведення високоендотермічной реакції піролізу вуглеводнів в ацетилен розрізняють чотири методи.
1). Регенеративний піроліз в печах з вогнетривкої насадкою; її спершу розігрівають топковим газами, а потім через розпечену насадку пропускають піролізуемое сировину. Ці періоди чергуються.
2). Електрокрекінг за допомогою вольтової дуги, коли вуглеводневу сировину піддають піролізу в електродугових печах при напрузі між електродами 1000 В. Витрати електроенергії доходять до 13 000 кВт-год на 1 т ацетилену, що складає головний недолік методу.
4). Окислювальний піроліз, при якому екзотермічна реакція горіння вуглеводнів і ендотермічний процес піролізу поєднані в одному апараті.
Всі ці способи піролізу вуглеводнів на ацетилен застосовують в промисловості, але найбільш економічним з них є окислювальний піроліз.
4. Фізико-хімічні основи процесу одержання ацетилену методом термоокислению піролізу метану.
З метану та інших парафінів ацетилен отримують шляхом високотемпературного піролізу за наступними оборотним реакцій:
Ці реакції ендотермічну, і їх рівновагу зміщується вправо тільки при 1000--1300 ° С. Однак при практичному здійсненні процесу з метою його прискорення потрібна вища температура: 1500--1600 ° С для метану і 1200 ° С для рідких вуглеводнів.
Подібно піролізу на олефіни, реакції утворення ацетилену мають радикально-ланцюговий механізм, причому ланцюг перетворень метану і етану можна уявити приблизно так:
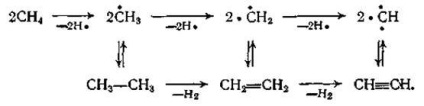
В отриманому газі крім нижчих парафінів і олефінів міститься невелика кількість бензолу і ацетиленових вуглеводнів - метилацетилену СН3 --ССН, а також вінілацетилену СН2 = СН - ССН, диацетилу СНС - CCH та ін.
Отримання ацетилену даним методом ускладнюється побічною реакцією його розкладання на вуглець і водень. Вона стає помітною при 1000 ° С і досягає значної швидкості при 1200--1600 ° С, т. Е. При температурі, необхідної для отримання ацетилену. В результаті спостерігається система послідовних реакцій, при якій утворюється ацетилен розкладається на водень і вуглець (сажу):
Як і в інших подібних випадках, регулювання виходу проміжного продукту може бути досягнуто зменшенням ступеня конверсії вихідного вуглеводню в результаті зниження часу контакту. Знайдено, що хороший вихід ацетилену при невеликому освіту сажі можна отримати при ступеня конверсії вихідного вуглеводню 50% і часу його перебування в зоні реакції 0,01 с. Щоб уникнути подальшого розкладання ацетилену необхідна швидка «гарт» реакційних газів (впорскування води), при цьому температура різко знижується до такого рівня, при якій розпаду ацетилену не відбувається.
При нестачі кисню і високої температури згоряння метану відбувається в основному за реакцією:
Вона протікає дуже швидко, і освіту ацетилену (як більш повільний процес) починається лише в зоні, практично позбавленою кисню. Там же відбувається конверсія оксиду вуглецю
Причому співвідношення водню, оксидів вуглецю та водяної пари виявляється близьким до цієї рівноваги водяного газу. У практичних умовах близько 1/3 кисню витрачається на освіту води, 10-15% на СО2 і 50--55% на СО.
Оскільки процес протікає в автотермічний режимі, для підтримки температури 1500 ° С, необхідної для розкладання метану, співвідношення початкових обсягів СН4 і О2 має становити 100: (6065), що знаходиться поза межами вибуховості цих сумішей. Небезпечні концентрації можуть виникнути лише під час змішування, проведеного при досить високій швидкості і турбулентності потоку газів. Саме горіння метану характеризується деяким періодом індукції, тривалість якого залежить від температури і тиску. Для метано-кисневих сумішей зазначеного вище складу при атмосферному тиску і 600 ° С період індукції складає 2с, що обмежує час від змішування попередньо підігрітих газів до їх попадання в пальники, де відбувається самозаймання суміші. Швидкість течії газу в соплі пальника (100 м / с) повинна бути вищою за швидкість поширення полум'я, щоб виникло полум'я не поширювалося в зворотному напрямку. У той же час при стабільному режимі горіння швидкість газу не повинна бути вищою за швидкість гасіння полум'я, щоб воно не відривався від пальника. При турбулентному потоці сталого горіння сприяють підведення додаткової кількості кисню в зону горіння (так званий стабілізуючий кисень), а також многосопловой пристрої з безліччю смолоскипів горіння, стабілізується один одного.
Технологічна схема отримання ацетилену окислювальним піролізом метану зображена на рис. 1. Кисень і метан підігрівають до 600-700 ° С в трубчастих печах 1 і 2, мають топки для спалювання природного газу. У реакторі 3 протікають вишерассмотренние процеси, причому гази виходять з нього після «загартування» водою при 80 ° С і проходять для уловлювання сажі порожнистий водяний скрубер 4 і мокропленочний електрофільтр 5. Гази охолоджують водою в холодильнику 6 безпосереднього змішання, після чого їх промивають в форабсорбере 7 невеликою кількістю диметилформаміду або N-метілпірролідона і направляють в газгольдер 8. Вода, що стікає з гідравлічного затвора реактора і з сажеулавлівающіх апаратів, містить 2-3% сажі, а також малолетучие ароматичні з'єдн ня. Вона вступає у відстійник 9, з верху якого сажу і смоли збирають скребками та направляють на спалювання. Воду з відстійника повертають в реактор як «гартівний агент», а її надлишок йде на очистку, ніж створюється замкнута система водооборота без скидання токсичних стічних вод.
Газ з газгольдера 8 стискається компресором 10 до тиску 1 МПа, проходячи після кожного ступеня холодильники і сепаратори, не показані на схемі. У абсорбере 11 він промивається диметилформамидом або N-метілпірролідона, а непоглотівшійся газ (Н2. СН4. СО, СО2) проходить скрубер 12, де при зрошенні водним конденсатом вловлюється віднесений їм розчинник. Після цього газ можна використовувати в якості синтез-газу або палива.
Розчин в кубі абсорбера 11 містить ацетилен і його гомологи, а також значна кількість близького до них по розчинності діоксиду вуглецю з домішкою інших газів. Він проходить дросельний вентиль 13 і надходить в десорбер 14 першого ступеня. За рахунок зниження тиску до 0,15 МЦА і нагрівання куба до 40 ° С з розчину десорбируются ацетилен і менш розчинні гази. Ацетилен при своєму русі вгору витісняє з розчину діоксид вуглецю, який разом з іншими газами і частиною ацетилену виходить з верху десорбера, попередньо відмиваючи від розчинника водним конденсатом. Ці гази повертають на компримування. Концентрований ацетилен виводять із середньої частини десорбера 14, промивають в скрубері 15 водою і через Вогнеперепинювачів 16 виводять з установки.
Кубову рідина десорбера 14, що містить деяку кількість ацетилену і його гомологів, направляють в десорбер 18 другого ступеня, підігріваючи попередньо в теплообміннику 17. За рахунок нагрівання куба до 100 ° С з розчину отгоняются все гази, причому із середньої частини колони йдуть гомологи ацетилену, що направляються потім на спалювання, а з верху - ацетилен з домішкою його гомологів, що повертається в десорбер першого ступеня. В розчиннику поступово накопичуються вода і полімери, від яких його звільняють на установці регенерації, що не зображеної на схемі. Отриманий на установці концентрований ацетилен містить 99,0--99,5% основної речовини з домішкою метилацетилену, пропадієну і діоксиду вуглецю (по 0,1-0,3%).
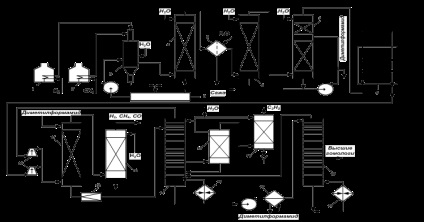
Мал. 1. Технологічна схема отримання ацетилену окислювальним піролізом метану
1, 2 - трубчасті печі; 3 --реактор; 4 - скрубер-сажеуловітель; 5 - електрофільтр; 6 - холодильник; 7 - форабсорбер; 8 - газгольдер; 9 - відстійник; 10 - компресори; 11-- абсорбер; 12, 15 - скрубери; 13 - дросельний вентиль; 14, 18 - десорбера; 16 --огнепреградітель; 17 - теплообмінник; 19 - кип'ятильники;