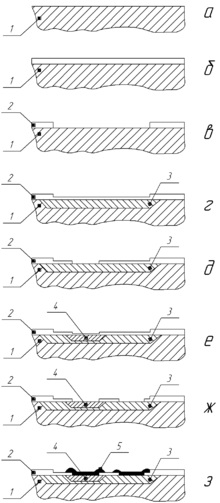
Виготовлення транзистора по планарной технології [1]
а - вихідна пластина; б - перший окислення; в - перша фотолітографічного обробка; г - створення базової області і друге окислення; д - друга фотолітографічного обробка; е - створення емітерний області і третє окислення; ж - третя фотолітографічного обробка; з - металізація.
1 - Напівпровідник з електропровідністю n-типу; 2 - маскує плівка діоксиду кремнію; 3 - область бази; 4 - область емітера; 5 - металева плівка (електроди).
На вхід технології надходять пластини, звані підкладками. Склад матеріалу підкладок, кристалічна структура (аж до міжатомних відстаней в підкладках для сучасних процесорів) і кристалографічна орієнтація строго контролюються. В ході технологічного процесу в при поверхневому шарі напівпровідникового матеріалу, що є підкладкою або нанесеного на підкладку, створюють області з різним типом або величиною провідності, яка визначається в кінцевому рахунку різною концентрацією донорних і акцепторних домішок, а також матеріалом шару. Поверх шару напівпровідникового матеріалу, з використанням в потрібних місцях прошарків діелектричного матеріалу, наносяться шари провідного матеріалу, що утворює контактні площадки і необхідні з'єднання між областями. Області і шари провідника, напівпровідника і діелектрика в сукупності утворюють структуру напівпровідникового приладу або інтегральної мікросхеми.
Особливість планарной технології полягає в тому, що після завершення кожної технологічної операції, відновлюється плоска (планарная) форма поверхні пластини, що дозволяє створювати досить складну структуру, використовуючи кінцевий набір технологічних операцій.
Планарная технологія забезпечує можливість одночасного виготовлення в єдиному технологічному процесі величезного числа дискретних напівпровідникових приладів або інтегральних мікросхем на одній підкладці, що дозволяє істотно знизити їх вартість. Також в разі виготовлення на одній пластині ідентичних приладів параметри всіх приладів виявляються близькими. Обмежувачем є тільки площа підкладки, тому діаметр підкладок у міру розвитку технологій виробництва підкладок прагнуть збільшувати.
Для контролю якості виконання проміжних операцій на підкладці, як правило, виділяють кілька малих областей (зазвичай в центрі і на периферії), на яких в ході штатного технологічного процесу формуються тестові провідні доріжки та елементарні прилади (конденсатори, діоди, транзистори і т.п. ). У цих же областях формують контактні площадки відносно великій площі для тестування придатності пластин перед скрабірованіе (поділом на окремі прилади). Для суміщення зображень при фотолітографії також в спеціально виділеній області формуються знаки суміщення, подібні до тих, які можна зустріти на багатобарвним друкованої продукції.
Основні технологічні операції
літографія
Основні технологічні операції, які використовуються в планарной технології, засновані на процесі літографії (фотолитографии). Застосовуються наступні методи:
Прийоми застосовуваної фотолитографии можуть бути сканирующими і проекційними; контактними, безконтактними, і на мікрозазори. (Дивись Іммерсійна літографія). Також може бути обмежено застосований метод радіаційно-стимульованої дифузії.
ланцюжок операцій
Технологічний ланцюжок складається з серії циклів (до декількох десятків), що включають в себе наступні основні операції (в порядку проходження):
- підготовка підкладки: застосовується механічна і хімічна полірування для отримання плоскої поверхні без механічних дефектів (виконується 1 раз, при надходженні підкладки в техпроцес);
- формування на поверхні підкладки шару необхідного матеріалу із заданою структурою: епітаксіальне нарощування. осадження діелектричних або металевих плівок (операція виконується не в кожному циклі);
- створення на поверхні підкладки захисного шару: в разі кремнієвих підкладок для цього використовується окислення поверхні, для здешевлення процесу, а також у разі інших підкладок, часто використовується епітаксіальне нарощування шару діоксиду або нітриду кремнію, або іншого матеріалу з низьким коефіцієнтом дифузії легуючих домішок. Товщина шару підбирається так, щоб за час, необхідний для створення легованої області необхідної конфігурації в підкладці, легуючий елемент не досяг підкладки крізь захисний шар;
- нанесення шару фоторезиста. володіє стійкістю до використовуваних Травители;
- суміщення зображень по знакам суміщення і експонування малюнка вікон на шар фоторезиста (виконується на степперах);
- підбурювання виключно засвічених (або незасвічені-залежить від типу фоторезиста) ділянок шару фоторезиста;
- підбурювання захисного шару з підкладки на ділянках, які не закритих фоторезистом;
- видалення залишків шару фоторезиста;
- можлива операція: впровадження легуючих домішок нерідко проводять в двохстадійному процесі, розділяючи фази загонки домішки в приповерхневих область і розгону загнаної домішки за необхідним обсягом (відпалу); загонками проводиться шляхом локальної (з поверхні або з газової фази) дифузії або іонної імплантації легуючих домішок через вікна в захисному шарі в поверхню підкладки; режими дифузії (імплантації) підбираються так, щоб за час цієї та всіх наступних технологічних операцій розмір легованої області досяг необхідних розмірів за площею і глибиною, а порушена радіацією при іонному легуванні кристалічна решітка відновилася;
- можлива операція: полум'яне або хімічне травлення поверхні підкладки для видалення надлишків шару раніше обложеного матеріалу.
- полум'яне або хімічне травлення поверхні підкладки для видалення захисного шару (виконується не в кожному циклі).
- планарізація [2] (згладжування нерівностей) поверхні перед переходом до нового циклу, наприклад за допомогою процесу CMP.
Основні цикли, що виконуються при створенні напівпровідникових приладів, такі:
- формування областей р-типу (локальне впровадження домішок)
- формування областей n-типу (локальне впровадження домішок)
- формування провідних доріжок і контактних площадок (видалення надлишків шару металу). Див. Також Омічний контакт.
Схеми чергування операцій і циклів бувають досить складні, а їх кількість може вимірюватися десятками. Так, наприклад, при створенні мікросхем на біполярних транзисторах з колекторної ізоляцією, з комбінованою ізоляцією (ізопланар-1,2; поліпланар) і в інших схемах, де необхідно або бажано забезпечити зниження опору колектора і підвищення швидкодії,) спочатку виконується оксидування, фотолітографія і дифузія під похованих n + шар, потім нарощується епітаксіальний шар напівпровідника ( "захораниванием") і вже в епітаксиальні шарі створюються конкретні елементи мікросхеми. Після цього поверхню пластини знову ізолюють, виконують контактні вікна, і наносять провідні доріжки та контактні площадки. У складних мікросхемах контактні доріжки можуть виконуватися в декілька рівнів з нанесенням між рівнями діелектричних прошарків, знову ж таки з витравленими вікнами.
Порядок циклів в першу чергу визначається залежностями коефіцієнтів дифузії домішок від температури. Намагаються спочатку виробляти загонками і розгонку домішок менш рухливих, і для скорочення часу процесу використовувати більш високі температури. Потім при менших температурах заганяють і розганяють більш рухливі домішки. Це пов'язано з швидким (експоненціальним) падінням коефіцієнта дифузії при зниженні температури. Наприклад, в кремнії спочатку при температурі до
950 ° C створюють області р-типу леговані бором і тільки потім при температурі менше
750 ° C створюють області n-типу, леговані фосфором. У разі інших легуючих елементів і / або інших матриць номінали температур і порядок створення легованих областей може бути різним, але завжди при цьому намагаються дотримуватися правила "зниження градуса". Створення доріжок завжди виконується в завершальних циклах.
Крім діфузіонной легування і розгону можуть застосовуватися методи радіаційної трансмутації кремнію в алюміній і фосфор. При цьому проникаюча радіація крім запуску реакцій трансмутації помітно пошкоджує кристалічну решітку підкладки. Легування пластини йде по всій площі і по всьому об'єму матеріалу, розподіл утворюються домішок визначається інтенсивністю проникаючого в товщу речовини випромінювання і тому підкоряється закону Бугера-Ламберта:
N = N0 * e -ax. де N - концентрація домішки;
N0 - концентрація домішки на поверхні; a - коефіцієнт поглинання випромінювання; x - відстань від опромінюваної поверхні;
Для легування зазвичай використовували злитки кремнію не розрізаний на пластини. В цьому випадку профіль розподілу домішки по діаметру пластини описується транспозицией експонент з максимумом на периферії пластини і мінімумів в центрі пластини. Цей метод має обмежене застосування для виготовлення спеціальних приладів з високоомного кремнію.
Завершальні операції при виробництві мікросхем
Скрайбування
По завершенні операцій по формуванню приладів на пластині виробляється поділ пластини на малі кристали. містять єдиний готовий прилад.
Спочатку поділ пластини на окремі кристали велося шляхом процарапуванії її на глибину 2/3 від товщини пластини алмазним різцем з подальшим розколюванням по процарапанной лінії. Цей принцип поділу дав назву всій операції поділу пластин на кристали: «скрайбірованіе» (або скрабірованіе від англ. Scribe - дряпати).
В даний час скрабірованіе може виконуватися як з прорізанням на повну товщину пластини з утворенням окремих кристалів, так і на частину товщини пластини з подальшим розколюванням на кристали.
Скрайбування з деякою натяжкою можна віднести до завершальних етапах планарной технології.
Прорізання може виконуватися різними шляхами:
- Скрайбування алмазним різцем - процарапиваніє пластини вздовж однієї з кристалографічних осей для подальшого розламування за ризиками подібно до того, як діють при різанні скла. Так на кремнієвихпідкладках розломи найкраще виходять по площинах спайності. В даний час метод є застарілим і практично не використовується;
- Розколювання локальним термоудара (застосовується мало);
- Різка кільцевої пилкою з зовнішньої ріжучої крайкою: установка схожа на установку для різання злитка на пластини, але діаметр диска значно менше і ріжучакромка виступає за затискачі не більше ніж на півтори глибини ризики. Це зводить до мінімуму биття і дозволяє збільшити частоту обертання до 20-50тис. обертів за хвилину. Іноді на вісь надягають декілька дисків для одночасного створення декількох рисок. Спосіб дозволяє прорізати пластину на всю товщину, але зазвичай використовується для процарапуванії з подальшим розколюванням.
- Хімічне скрабірованіе - це скрабірованіе шляхом наскрізного хімічного травлення. Для проведення операції попередньо робиться фотолітографія з формуванням вікон на розділових ділянках з обох сторін пластини і витравлюються розділові області. Різновидом даного методу є наскрізне анізотропне травлення, де використовується різниця в швидкості травлення в різних напрямках кристалографічних осей. Основні недоліки обмежують застосування методу - складність поєднання малюнка вікон для травлення обох сторін пластини і бічне витравлювання кристалів під маскою. Спосіб дозволяє як протравить пластину на частину товщини, так і на всю товщину.
- Різка сталевими полотнами або дротами - полотна або дріт труться об пластини, на місце зіткнення подається абразивна суспензія. Існує ризик псування готових структур лопнули полотном або дротом. Коливання складу суспензії, механічні перекоси в обладнанні також можуть призводити до появи шлюбу. Метод використовувався в дрібносерійних виробництвах і лабораторіях. Спосіб дозволяє прорізати пластину всю товщину, але зазвичай використовується для процарапуванії з подальшим розколюванням.
- різання лазерним променем: освіта рисок відбувається в результаті випаровування матеріалу підкладки сфокусованим лазерним променем. Застосування методу обмежується товщиною пластин, а так як більший діаметр пластин вимагає більшої товщини для збереження необхідної жорсткості не завжди використовується наскрізне поділ (менш 100 мкм - можливо різання, від 100 до 450мкм тільки скрайбірованіе). При наскрізному поділі не потрібно подальша ломка пластини на кристали. Не рекомендується використовувати даний метод для різання пластин, що містять арсенід галію через виділення високотоксичних сполук. В СРСР для цього методу в основному використовувалися лазери з алюмо-ітрієві граната і рубіна. Основною проблемою при використанні різання лазерним променем є захист готових структур від крапель розплавленого і конденсації на них іспарённого матеріалу підкладки. Оригінальним способом вирішення цієї проблеми є використання при лазерного різання як фокусирующего світловода і одночасно холодоагенту тонкого шнура води подається під високим тиском [3].
Після прорізання рисок пластини поділяють на кристали. Існує три основні методи:
- Метод подпружиненного ролика: пластину укладають в поліетиленовий пакет і розміщують на товстому пружному гумовому підставі ризиками вниз і оператор прокатує уздовж рисок підпружиненим роликом. Якість розламування залежить від того на скільки напрямок руху ролика паралельно ризиків, при відхиленні можливо розколювання не по ризикам і псування кристалів.
- Розламування на півсфері: пластини обжимаються еластичною мембраною по сферичної поверхні. На мембрану тиснуть або гідравлічним способом, або стисненим повітрям. При поділі цим способом пластин діаметром понад 76 мм різко збільшується відсоток браку.
- Прокатка між двома циліндричними валиками. Пластина на липкій стрічці-носієві стискають сталевим і гумовим валиком, які обертаються, в результаті деформації пружного гумового валика до пластині прикладається изгибающее зусилля.
Кріплення кристалів до корпусу
Після скрайбування кристали приєднують до основи корпусу:
- методом приклеювання - використовуються клеї на основі епоксидної смоли, з часом деградує: гірше проводить тепло, стає крихкою, з'єднання стає неміцним. Даний метод в даний час не використовується.
- метод евтектичного сплаву: на керамічне підставу корпусу і на зворотну сторону пластини перед поділом на кристали наноситься тонкий шар золота. У місці кріплення кристала поміщається золота фольга, кристал кладуть на підставу корпусу, підігрівають до 380 ° (температура евтектики системи кремній-золото 385 °) і прикладають вертикальне зусилля. Висока вартість дозволяє використовувати метод тільки для схем спецпризначення.
- при герметизації пластмасою кристали з приварений арматурою розміщують на стрічці-носієві.
- з'єднання стеклами - зважаючи на складність підбору скла з низькою температурою розм'якшення і температурним коефіцієнтом лінійного розширення, відповідним використовуваних матеріалів даний метод для тонкоплівкової технології малопридатний (годиться для гібрідниx і товстоплівкова інтегральних схем)
- метод «перевернутого кристала» - при використанні об'ємних висновків одночасно приєднуються і кристал і все висновки.
Приєднання висновків до кристалу
методи приєднання висновків:
- термокомпрессіонной зварювання
- ультразвукове зварювання
- непрямого імпульсного нагріву
- зварювання здвоєним електродом
- лазерна точкове зварювання
- електронно-променеве зварювання
- бездротовий монтаж елементів з об'ємними висновками
При тестуванні контролюється якість кріплення висновків, а також стійкість приладів (крім негерметичних) до екстремальних кліматичних умов на стенді тепла і вологи і механічних впливів на ударному і вібростенді, а також їх електричні властивості. Після тестування прилади фарбують і маркують.
Література по темі